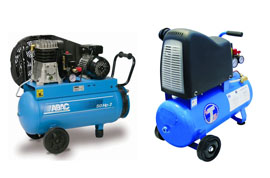
Компрессором называют машину, осуществляющую операции по сжатию и перемещению газов. По принципу действия выделяют объёмные, динамические и струйные компрессоры. Самыми распространёнными являются относящиеся к классу объёмных машин поршневые компрессоры.
Первый образец поршневого компрессора был разработан и опробован в 18 веке изобретателем И. И. Ползуновым в металлургическом производстве. Вплоть до начала 20 века компрессоры этого типа были единственными машинами для подачи сжатого воздуха. С появлением в 60-х годах 20 века новых самосмазывающихся и имеющих малый коэффициент трения материалов, разрабатываются и внедряются устройства без смазки рабочих цилиндров.
Устройство и принцип действия
Основная рабочая часть компрессора представляет собой цилиндр, в стенках которого размещаются всасывающий и нагнетательный клапаны. Клапаны открываются автоматически из-за перепада давления между полостью цилиндра и всасывающей или нагнетательной камерой. Внутри цилиндра перемещается поршень, который в начале хода захватывает воздух, поступающий из всасывающей камеры, и сжимает его. В конце хода поршня достигается давление газа, необходимое для открытия нагнетательного клапана и сжатый воздух поступает в ресивер (накопительную ёмкость).
Перемещение поршня осуществляется за счёт работы привода – электрического мотора, двигателя внутреннего сгорания или паровой турбины. Передача вращения от привода поршню может быть прямая или через ремённую передачу.
И всё же основным и неизменным для любого поршневого компрессора, независимо от типа привода или его производительности, остаётся принцип сжатия газа в цилиндре. В процессе сжатия происходят дополнительные затраты мощности на преодоление трения между движущимся поршнем и цилиндром, а также перетечки газа между рабочими полостями, что снижает производительность аппарата.
Для минимизации этих эффектов поршень при перемещении не касается стенок цилиндра, а образовавшийся зазор перекрывается уплотнительными кольцами, расположенными на поршне. По типу уплотнительного узла различают компрессоры со смазкой цилиндра и без неё. Рассмотрим различия таких аппаратов.
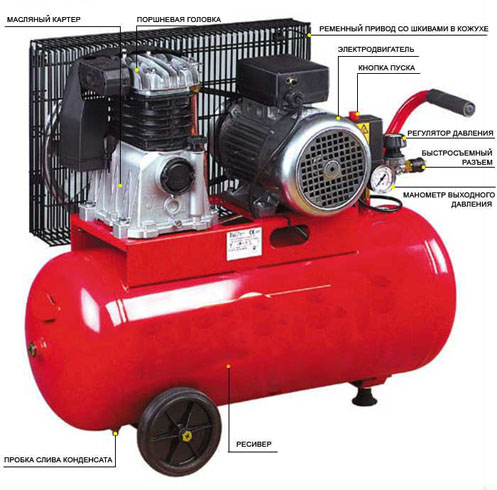
Компрессор масляный
Отличия в конструкции
Для компрессора со смазкой цилиндра в отличие от безмаслянного необходима система подачи масла, состоящая из лубрикатора, насоса, и системы трубок. Конструкция цилиндра также усложняется, добавляются отверстия в крышке и на стенках цилиндра для подачи смазки.
Уплотнительные кольца масляного аппарата являются бесконтактными, механическое трение между ними и стенками цилиндра почти отсутствует за счёт смазки. Препятствием для перетечки газа между кольцом и стенкой цилиндра является гидравлическое сопротивление масла. Кольца разрезные, замок прямой или наклонный. На поршень в масляных компрессорах также устанавливаются маслосъёмные кольца, имеющие пазы и сверления для отвода масла.
У безмасляных агрегатов на поршень устанавливаются два вида колец – направляющие и уплотнительные. Направляющие предотвращают касание поршнем стенок цилиндра, а уплотнительные препятствуют утечкам газа. Кольца разрезные, с прямоугольным сечением, стыки прямые или с нахлёстом. Для изготовления колец используют различные полимерные композиции, фоторопласт и соединения с графитом. Так как кольца контактные, то они достаточно быстро изнашиваются и увеличиваются потери. Ресурс колец значительно ниже чем у машин со смазкой и для высоких давлений может составлять всего 100-200 часов работы.
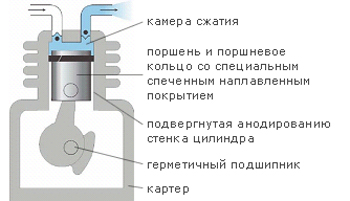
Безмасляный компрессор
Отличия при эксплуатации
Для масляного агрегата требуется постоянный контроль наличия смазки, причём масло должно быть специальной марки. Смазку необходимо периодически добавлять и заменять. Для мобильных масляных установок необходимо соблюдать горизонтальное положение машины во избежание разлива масла из бака.
Безмасляные машины избавлены от проблем с маслосистемой, но требуют более частой замены поршневых колец.
Операции по очистке воздушных фильтров, проверке воздушных соединений и обслуживанию регулирующей и запорной аппаратуры идентичны для обоих видов машин.
Отличия по назначению
Для понимания отличий по этому признаку, разделим рассматриваемые аппараты на две большие группы по критерию производительности: бытовые и полупромышленные с производительностью до 1000 л/мин. и промышленные с большей производительностью.
Первые используются как отдельные устройства для подачи воздуха пневмоинструментам, холодильным агрегатам и небольшим установкам различного назначения. Устройства этой группы производят сжатие атмосферного воздуха и выбор типа компрессора зависит только от необходимой производительности и вида проводимых работ. Для кратковременных периодических работ вполне подходят безмасляные машины, стандартный цикл (работа/пауза) которых составляет 2,5/7,5 минут. Компрессор со смазкой цилиндров выбирают для проведения длительных по времени работ, например, для работы отбойным молотком или покраски больших зданий.
У группы промышленных устройств, которые используются в составе компрессорных станций, есть два дополнительных критерия:
- Тип сжимаемого газа. Нельзя использовать масляные компрессоры для некоторых газовых смесей, потому что при их контакте с маслом может произойти взрыв.
- Периодичность обслуживания. Выбор в первую очередь падает на масляные машины с более длительным ресурсом, а контроль масла делается дистанционно.
В заключение отметим различия в цене двух видов устройств. Из-за наличия дополнительного контура масляной смазки, при одинаковом показателе производительности, масляный компрессор будет стоить дороже безмасляного.